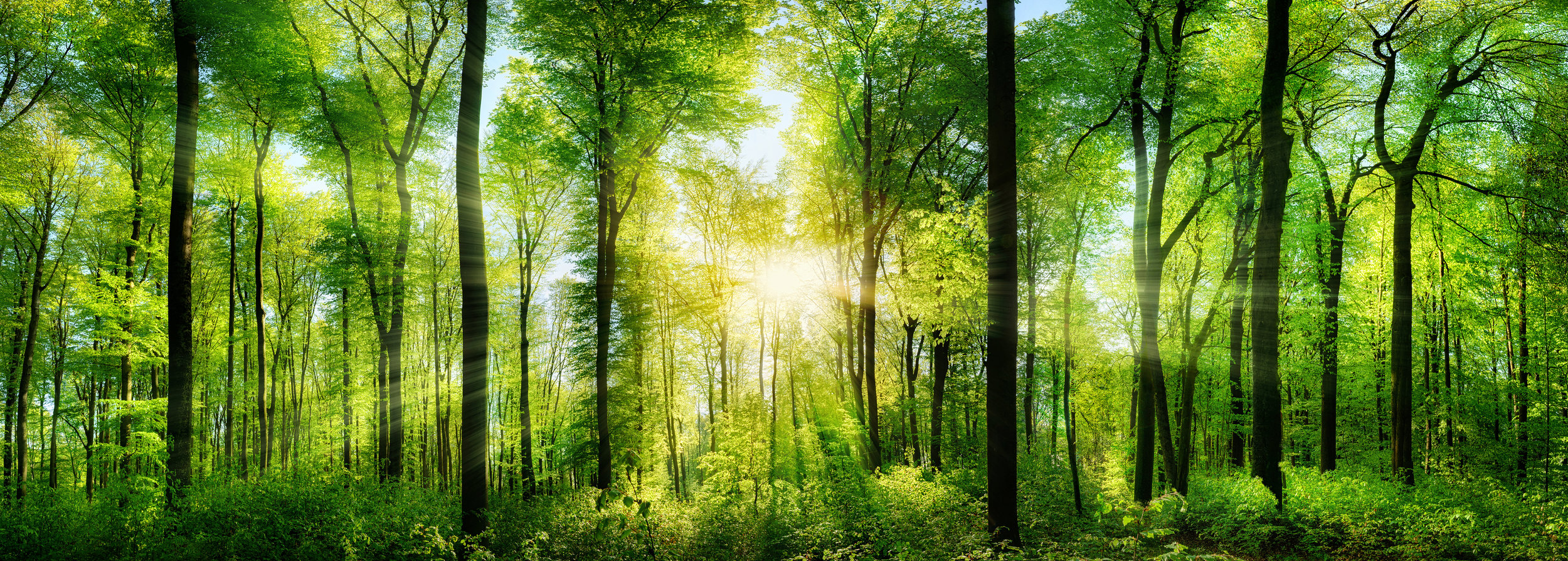
EarthCoating® is a mineral-enriched resin barrier coating, used as a drop-in replacement to 100% plastic coatings for paper-based barrier packaging applications.
Smart Planet Technologies has developed and commercialized EarthCoating, a range of mineralized functional barrier coatings, to produce barrier coatings that outperform conventional barrier coatings (polyethlene, BioPBS) while improving the environmental footprint of the package.
EarthCoating has three key advantages of plastic coatings:
Up to 51% less plastic
Lower cost
EarthCoating is compatible with paper recycling systems, resulting in paper based packaging that is universally recyclable in conventional paper recycling systems.
Background
Historically, minerals such as calcium carbonate were used as a filler in plastic coatings, typically up to 10% by weight. Beyond that amount, the coating’s performance was compromised, and it was difficult to run the blend in extrusion coating equipment. The calcium carbonate used was of a low grade, as the priority was to lower cost.
Smart Planet discovered that if you use minerals that are more refined, along with different combinations of particle sizes, and enhance the dispersion of the minerals in the coating, there are dramatic improvements in the performance of the coating as well as many environmental advantages. EarthCoating is comprised of up to 51% mineral content by weight, yet runs at full line speeds in extrusion coating equipment. This results in less plastic and lower cost, at far more favorable levels than a 10% filler. In addition, the refined mineral formulation improves functional coating performance with improved barrier performance and heat sealing.
The most dramatic discovery was found in its recyclability. Clay coating is commonly applied to paper packaging and is considered an inert ingredient for paper recycling. The high mineral content in EarthCoating makes it perform as a clay coating, not a plastic coating for the purposes of recycling.
So, you wind up with the best of both worlds: A coating that acts as a polymer barrier coating for the purposes of packaging performance, but acts as a clay coating for the purposes of recycling. By doing so, the problem of poor recyclability of barrier-coated paper packaging has been solved.
Key features:
Up to 51% less plastic than conventional plastic coatings
Cost savings opportunities as EarthCoating is lower in cost than polyethylene
Paper packaging with EarthCoating is fully compatible with conventional paper recycling systems. Packaging with EarthCoating has been rated AAA for recyclability by Europe’s Der Grune Punkt, and qualified for collection in the coveted Path 13 along with uncoated paper.
Improved Barrier and Heat Seal performance to 100% polyethylene
EarthCoating is classified along with clay coatings for the purposes of paper recycling, therefore paper packaging with EarthCoating is universally compatible with paper recycling systems
EarthCoating is applied using the same extrusion coating equipment as conventional plastic coatings, with no new equipment needed, and at full line speeds
Package converting using paper and paperboard with EarthCoating runs on conventional converting equipment at full line speeds
No change to the package aesthetics
EarthCoating can be provided either as a masterbatch formulation, to be blended with polymer in line at the extruder, or as a premixed compound.
EarthCoating technology can be used with BioPBS to produce mineralized barrier coatings that are industrially compostable, biobased, and universally recyclable.
EarthCoating is commercialized across many barrier-coated paper and paperboard packaging applications including paper cups, food trays, folding cartons, take out boxes, labels, liners, corrugated packaging, flexible bags.
To learn more, download our EarthCoating One Sheet and give us a call today to discuss your next project.
FEATURES & BENEFITS
ENVIRONMENT
Recyclability
Traditionally, mixed grade paper barrier packaging applications such as paper cups, take out boxes, folding cartons, etc. are coated with 100% polyethylene and other similar materials, which make them very difficult to recycle. The plastic coating breaks into large sturdy flakes that float along with the fibers and clog the screening process, like tree leaves clogging a storm drain. Typically if a bale of mixed paper has more than 3% of plastic coated paper, and is put into the pulper, the screens can become clogged, causing a shutdown, and potentially damaging equipment.
By contrast, packaging applications made with EarthCoating® can be easily processed using conventional paper recycling equipment. Like a clay coating, EarthCoating is denser than water because of the mineral content and falls to the bottom of the pulper with clay coating, paper clips, staples, and other items to be removed in the recycling process. That leaves the paper fibers to be collected cleanly from the pulper without barrier coating contamination. Recycling tests of packaging with EarthCoating is done successfully with bales containing 100% packaging coated with EarthCoating, and the materials are qualfied for collection in uncoated paper grades.
Reduction of Plastic
The mineral content in EarthCoating® offsets up to 51% of the plastic by weight that would otherwise be found in a conventional plastic coating.
Energy Use Savings
Energy savings are realized whenever paperboards are recycled. Paper tonnage which might otherwise be buried in US landfills may be collected and reused, resulting in reduced greenhouse gas emissions and energy savings.
For example, every ton of paper recycled can save the energy equivalent of 165 Gallons of gasoline. If the approximately 58 billion paper cups that are buried in US landfills each year were to be recycled, approximately 700,000 tons of paper would be recovered – resulting in energy savings equivalent to removing almost a quarter million cars from our roads.
PERFORMANCE
Superior Moisture Barrier
The minerals in EarthCoating® produce a tortuous path for moisture to pass through, resulting in better moisture vapor transmission rates (MVTR). Ask about our MVTR report.
Superior Heat Seal Performance
Mineralized resins absorb and dispel heat differently than neat polyolefins, resulting in better heat seal performance and fiber tear.
High Quality Print Surface
Unlike traditional polyethylene, EarthCoating® offers a high surface energy complete with a typical post-corona dyne level of 46, providing an excellent print surface for high quality graphics using digital, offset, flexo and rotogravure printing techniques.
ECONOMICS
Material Cost Savings
The use of low cost minerals in the resin blend, offsetting traditional 100% plastic resins, may be used to create material cost savings compared to neat polyolefin or bio-resin coatings.
Source Reduction Enabled by Superior Performance Yields Cost Savings
Compared to traditional plastic coatings, EarthCoating® provides superior barrier performance, which often results in an opportunity to down gauge coat weights, leading to source reduction and potential cost savings.
Post-Industrial Trimmings Rebate
Paper-based packaging applications coated with EarthCoating® are engineered for repulping through existing paper recycling streams, providing premium high value fibers without plastic contamination nor a laborious depolymerization process found in the effort to process traditional paperboards with 100% polyolefin coatings. As a result, industrial EarthCoating® trimmings are sought after at a premium value by recyclers, resulting in a potential rebate for supply chain vendors.
EARTHCOATING® COMPOUNDS
Refined Minerals 100% Polymer Resin
Refined minerals are blended into polyolefin resin, creating EarthCoating®, for extrusion coating onto papers and paperboards at high commercial line speeds using conventional extrusion coating equipment without any additional capital investment.
EarthCoating® compounds include:
EC-40: 40% Mineral / 60% LDPE - ideal for coffee cups, folding cartons, food trays, etc.
EC-51: 51% Mineral / 49% LDPE - ideal for coffee cups, folding cartons, food trays, etc.
EC-Bio: 38% Mineral / 35% BioPBS / 27% PLA - for biobased, recyclable and industrially-compostable paper-based packaging
EC-EU: 43% Calcium Carbonate / 57% LDPE - ideal for coffee cups, folding cartons, food trays, etc. meeting European Union design specification requirements.
EC-PP: 40% Mineral / 60% Polypropylene - ideal for microwave conditions
HyperBarrier: 40% Nano/CaCO3 / 60% LDPE- ideal for high barrier applications in flexible packaging
EC-70 Masterbatch: 70% Mineral/ 30% LDPE To be mixed inline on the extruder with 100% polyethylene to produce EC-40 or EC-51
EC-85 Masterbatch: 85% Mineral / 15% Polymer To be mixed inline on the extruder with PLA/BioPBS to produce EC-Bio.